Model NO.: 3CPV
Rotation Axis: Asynchronous Motor, 4.0kw
Tube Od of Chamfer/Squaring/Deburring: 6-80mm
Tube Od of Flaring: 6-80 mm
Tube Od of Beading: 6-75 mm
Trademark: Hartco
Transport Package: Wood
Specification: OD6-80mm
Origin: Shanghai
HS Code: 8461909000
Model NO.: 3CPV
Rotation Axis: Asynchronous Motor, 4.0kw
Tube Od of Chamfer/Squaring/Deburring: 6-80mm
Tube Od of Flaring: 6-80 mm
Tube Od of Beading: 6-75 mm
Trademark: Hartco
Transport Package: Wood
Specification: OD6-80mm
Origin: Shanghai
HS Code: 8461909000
3CPV Semi-automatic Tube End Finish MachineDescription: Semi-automatic Tube End Finish MachineModel: 3CPVApplication:Used for deburring,flaring,Beading for Inside and outside of metal round tube end.Introduce:Using the tube end-finishing machines, the ends can be prepared with a bead or flare, or simply deburred and squared. Each machine is capable of performing all of these functions -a change of tooling is all that is required to switch from one function to another.Main Specification:
- Dimensions: Long X Wide X High (excluding protruding parts) =660X1000X1230mm
- Weight: 500 kg
-
Power supply: 380V±10%, 50Hz/60Hz, three phase
- Power: 4 KW
- Air pressure: 0.4-0.8MPa;
- Clamping mode: pneumatic;
-
Clamping force: >=20KN;
- Rotation axis: asynchronous motor, 4.0kw;
-
Coaxial of rotation spindle with clamping shaft: ≤0.02 mm;
-
Rotation axis deflection: ≤0.01 mm;
Capacity:
- Tube OD of chamfer/squaring/deburring: Φ6-80mm;
-
Tube WT of chamfer/squaring/deburring: ≤10mm;
- Tube OD of flaring: Φ 6-80 mm;
- Tube WT of flaring:
Stainless steel 0.4 ~ 2.5mm, Aluminum alloy 0.5 ~ 3.5mm;
- Flaring method: eccentric inner diameter rotary swage;
- Tube OD of beading: Φ6-75 mm;
-
Tube WT of beading: stainless steel: ≤1mm, aluminum alloy: ≤ 2mm;
- Beading method: inner diameter rotary swage;
- Tube min clamp: 15mm (flare tube is based on material and wall thickness);
- Tube material: all kinds of titanium alloys, stainless steel, aluminum alloy;
Features:
- One clamping can be completed squaring, deburring, inside and outside chamfering at the same time.
- After quick change dies, it can complete the tube flaring processing and beading.
- Cylinder clamping function, make the fitting clamping tight. Clamping with buffer, avoid damaging the tube.
- Thin clamp and thin dies, the minimum length of tube is 15mm, which is the first and best level.
- Control of the feed cylinder is linkage with the clamp cylinder, the clamping cylinder is automatically clamped when the feed cylinder is started, and then spindle forward for processing, once finish, the spindle retreat, clamp cylinder automatically open.
-
Equipped asynchronous motor spindle, speed variable frequency control adjustment, is suitable for the processing of different materials.
- Tube feeding length positioning function, ensure tube process length and repeat precision.
- Flaring center is a eccentric shaft, one specification of the flaring center can make a variety of sizes, a variety of wall thickness of tube flaring processing.
- The dies for chamfer&deburing&squaring can be directly use flaring Dies, reducing dies specification, and reducing the time of replacing.
Main Components:
- The spindle on the top, opening is very good, especially suit for bended complex shaped tube.
- Variable frequency control of motor, to achieve the spindle high precision control.
- Clamp on the machine cabinet front, it can clamping minimum 15mm straight tube. The clamp is placed on the outside, the main shaft is located at the top, and the volume is less than the clamp shape, so the machine is very open, the tube end processing of complex tubing is guaranteed.
- The clever design chip groove in clamp, lead the dust smoothly into waste box.
- Double feed mode: cylinder feed and handwheel feed, control feed speed, make operation smoother and save physical power.
- Tube feed stopper: when the spindle forward, stopper automatic drop down. Feed length is adjustable, and can be mechanical lock.
- Spindle feed position:ensure consistency processing of feed, while ensuring the spindle and clamp non-interference.
- Organic glass protective cover/waste box, It is the best protection for personnel, and can collect the waste.
Tooling:
- Flaring center: Is a eccentric shaft, one specification of the flaring center can make a variety of sizes, a variety of wall thickness of tube flaring processing.
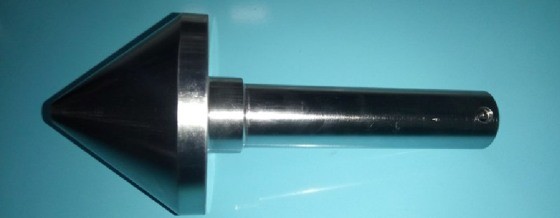
- Flaring dies: The dies for chamfer&deburing&squaring can be directly use flaring Dies, reducing dies specification, and reducing the time of replacing.
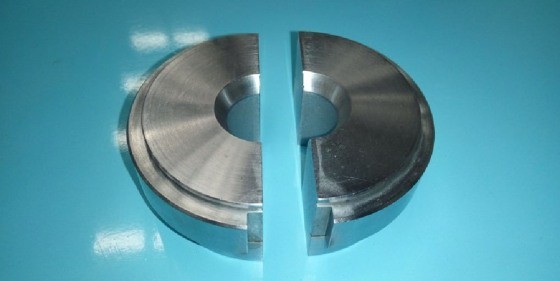
- Die adapter: used for installation of flaring dies or beading dies of small tube dimension.
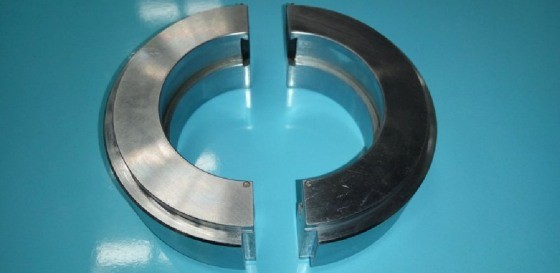
-
The squring&deburing head design is smart, the blade position can be adjusted, one set of blade can complete squring, deburing, chamfer for different tube dimension with wall thickness.Â
-
Beading head is used with beading tip or beading arbor, the minimum can complete the 6mm tube beading.Â
3CPV Semi-automatic Tube End Finish MachineDescription: Semi-automatic Tube End Finish MachineModel: 3CPVApplication:Used for deburring,flaring,Beading for Inside and outside of metal round tube end.Introduce:Using the tube end-finishing machines, the ends can be prepared with a bead or flare, or simply deburred and squared. Each machine is capable of performing all of these functions -a change of tooling is all that is required to switch from one function to another.Main Specification:
- Dimensions: Long X Wide X High (excluding protruding parts) =660X1000X1230mm
- Weight: 500 kg
-
Power supply: 380V±10%, 50Hz/60Hz, three phase
- Power: 4 KW
- Air pressure: 0.4-0.8MPa;
- Clamping mode: pneumatic;
-
Clamping force: >=20KN;
- Rotation axis: asynchronous motor, 4.0kw;
-
Coaxial of rotation spindle with clamping shaft: ≤0.02 mm;
-
Rotation axis deflection: ≤0.01 mm;
Capacity:
- Tube OD of chamfer/squaring/deburring: Φ6-80mm;
-
Tube WT of chamfer/squaring/deburring: ≤10mm;
- Tube OD of flaring: Φ 6-80 mm;
- Tube WT of flaring:
Stainless steel 0.4 ~ 2.5mm, Aluminum alloy 0.5 ~ 3.5mm;
- Flaring method: eccentric inner diameter rotary swage;
- Tube OD of beading: Φ6-75 mm;
-
Tube WT of beading: stainless steel: ≤1mm, aluminum alloy: ≤ 2mm;
- Beading method: inner diameter rotary swage;
- Tube min clamp: 15mm (flare tube is based on material and wall thickness);
- Tube material: all kinds of titanium alloys, stainless steel, aluminum alloy;
Features:
- One clamping can be completed squaring, deburring, inside and outside chamfering at the same time.
- After quick change dies, it can complete the tube flaring processing and beading.
- Cylinder clamping function, make the fitting clamping tight. Clamping with buffer, avoid damaging the tube.
- Thin clamp and thin dies, the minimum length of tube is 15mm, which is the first and best level.
- Control of the feed cylinder is linkage with the clamp cylinder, the clamping cylinder is automatically clamped when the feed cylinder is started, and then spindle forward for processing, once finish, the spindle retreat, clamp cylinder automatically open.
-
Equipped asynchronous motor spindle, speed variable frequency control adjustment, is suitable for the processing of different materials.
- Tube feeding length positioning function, ensure tube process length and repeat precision.
- Flaring center is a eccentric shaft, one specification of the flaring center can make a variety of sizes, a variety of wall thickness of tube flaring processing.
- The dies for chamfer&deburing&squaring can be directly use flaring Dies, reducing dies specification, and reducing the time of replacing.
Main Components:
- The spindle on the top, opening is very good, especially suit for bended complex shaped tube.
- Variable frequency control of motor, to achieve the spindle high precision control.
- Clamp on the machine cabinet front, it can clamping minimum 15mm straight tube. The clamp is placed on the outside, the main shaft is located at the top, and the volume is less than the clamp shape, so the machine is very open, the tube end processing of complex tubing is guaranteed.
- The clever design chip groove in clamp, lead the dust smoothly into waste box.
- Double feed mode: cylinder feed and handwheel feed, control feed speed, make operation smoother and save physical power.
- Tube feed stopper: when the spindle forward, stopper automatic drop down. Feed length is adjustable, and can be mechanical lock.
- Spindle feed position:ensure consistency processing of feed, while ensuring the spindle and clamp non-interference.
- Organic glass protective cover/waste box, It is the best protection for personnel, and can collect the waste.
Tooling:
- Flaring center: Is a eccentric shaft, one specification of the flaring center can make a variety of sizes, a variety of wall thickness of tube flaring processing.
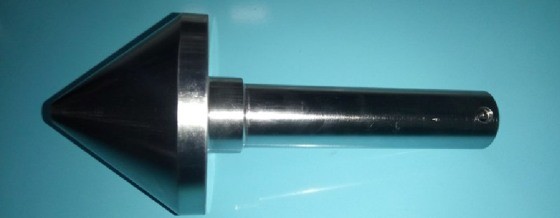
- Flaring dies: The dies for chamfer&deburing&squaring can be directly use flaring Dies, reducing dies specification, and reducing the time of replacing.
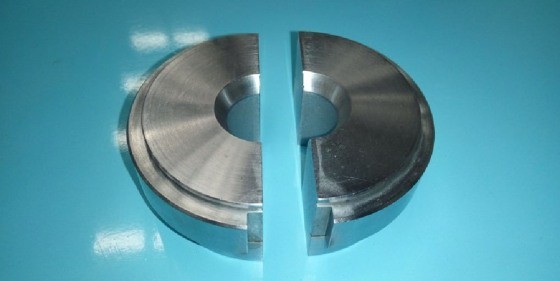
- Die adapter: used for installation of flaring dies or beading dies of small tube dimension.
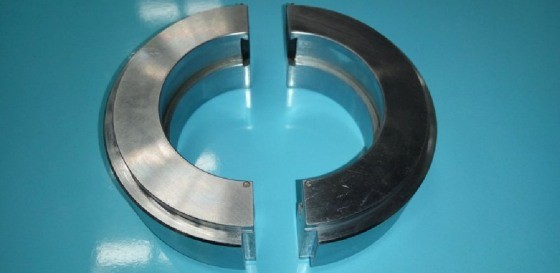
-
The squring&deburing head design is smart, the blade position can be adjusted, one set of blade can complete squring, deburing, chamfer for different tube dimension with wall thickness.Â
-
Beading head is used with beading tip or beading arbor, the minimum can complete the 6mm tube beading.Â